Introduction: The Global Supply Chain Crisis Unveiled
The global supply chain crisis, which first began to unfold in 2020, has now become a persistent and complex issue, continuing to affect economies, industries, and consumers worldwide. From delays in shipments and shortages of goods to rising prices and labor shortages, the disruptions in the supply chain have had far-reaching consequences. While the COVID-19 pandemic certainly acted as a catalyst, the crisis has exposed deep-rooted vulnerabilities and inefficiencies within global supply networks.
In this article, we will explore the deep causes behind the global supply chain disruptions, shedding light on the interplay of factors that led to the crisis. We will also identify which industries are most affected by these challenges and what the future holds for global supply chains in terms of resilience, recovery, and long-term changes.
Chapter 1: Understanding the Deep-Rooted Causes of the Global Supply Chain Crisis
The supply chain crisis cannot be attributed to a single cause; rather, it is the result of a complex web of interconnected factors. The pandemic might have triggered the disruptions, but the underlying issues go back years, if not decades.
1.1 The Impact of the COVID-19 Pandemic: A Global Shock
At the core of the supply chain crisis is the COVID-19 pandemic, which threw global logistics systems into disarray. The pandemic led to factory closures, port congestion, and shipping delays as governments imposed lockdowns, quarantines, and travel restrictions to curb the spread of the virus.
- Factory Shutdowns: Countries such as China, which are key players in global manufacturing, closed factories or operated at reduced capacity, impacting production lines for industries ranging from electronics to textiles.
- Port Congestion: Shipping ports, particularly in the United States and Europe, saw major congestion as fewer workers and limited infrastructure capacity caused a backlog of containers waiting to be unloaded. In the U.S., the Port of Los Angeles saw container ships waiting in line for weeks.
- Shipping Shortages: With restrictions on labor and transportation, shipping companies struggled to meet global demand. This led to a shortage of shipping containers, skyrocketing shipping costs, and delays in delivery times.
The pandemic illuminated the fragility of just-in-time supply chains and the world’s dependence on a few key manufacturing hubs and transportation routes.
1.2 Overreliance on Globalization and Just-in-Time Manufacturing
For decades, global supply chains have been built around the principles of globalization and just-in-time (JIT) manufacturing. The goal was to keep costs low by sourcing materials and components from different parts of the world, often in real-time, to meet immediate demand.
However, these practices, which seemed efficient during periods of stable global trade, have now proven to be highly vulnerable in times of disruption. The focus on cost-efficiency and inventory reduction left businesses ill-prepared to handle shocks like the pandemic. JIT manufacturing, in particular, relies on a seamless flow of goods and materials—something that proved impossible to maintain when the system was hit by supply-side shocks.
Furthermore, the heavy reliance on single-source suppliers—especially in key industries such as electronics and automotive manufacturing—made it difficult for businesses to switch suppliers or adapt quickly when one source failed.
1.3 Labor Shortages and Shifting Demographics
Labor shortages have also played a significant role in the ongoing supply chain crisis. Several factors have contributed to this phenomenon:
- Pandemic-related Health Concerns: Workers in critical industries, such as logistics, warehousing, and manufacturing, faced heightened health risks due to the pandemic, leading to significant absenteeism, strikes, and delays in production.
- Workforce Exodus: Many workers across the globe have retired early, changed careers, or left their jobs in the wake of the pandemic, contributing to a shortage of skilled labor in manufacturing, transportation, and logistics sectors. In the U.S., industries like hospitality, warehousing, and transportation have seen millions of workers quit or leave their positions in what has been called the “Great Resignation.”
- Migration Restrictions: In addition to domestic labor shortages, immigration policies and border closures disrupted the flow of migrant workers, who play a key role in many supply chain jobs in developed economies.
This shortage of workers in essential sectors like warehousing, manufacturing, and transportation has slowed production and led to bottlenecks in the supply chain.
1.4 Raw Material Shortages and Production Delays
Beyond labor, raw material shortages have been another critical factor exacerbating the supply chain crisis. The pandemic led to disruptions in the supply of key raw materials, such as semiconductors, lumber, oil, and steel.
- Semiconductor Shortage: One of the most visible impacts has been the global semiconductor shortage, which has affected industries like automotive, electronics, and consumer goods. As production plants in Asia shut down due to the pandemic, global demand for chips skyrocketed, leading to production delays and higher costs.
- Shipping Bottlenecks: Alongside material shortages, the shipping bottlenecks have compounded the problem. Delays in one part of the supply chain—such as a raw material shortage—can cause cascading disruptions in the manufacturing and distribution of finished goods.
1.5 Geopolitical Tensions and Trade Barriers
The rise of geopolitical tensions has also had a significant impact on global supply chains. The trade war between the U.S. and China, for instance, led to the imposition of tariffs and trade barriers that disrupted the free flow of goods and raw materials. Brexit created additional friction between the UK and the European Union, making trade more cumbersome.
The imposition of new tariffs, border controls, and export restrictions, especially on critical materials such as microchips and rare earth elements, has slowed down supply chain operations and increased costs.
1.6 Environmental Disasters and Climate Change
Environmental factors, such as natural disasters and the growing effects of climate change, have also played a role in supply chain disruptions. Typhoons, floods, wildfires, and hurricanes have all impacted manufacturing facilities, transportation routes, and agricultural production in various regions.
For instance, the 2021 Texas Winter Storm led to massive disruptions in oil production, affecting the global supply of petroleum and petrochemical products. Additionally, severe flooding in regions like Germany and China has damaged infrastructure and delayed deliveries.
Chapter 2: The Impact of the Global Supply Chain Crisis on Different Industries
The ripple effects of the global supply chain crisis have been felt across almost every sector of the global economy. However, some industries have been particularly hard-hit due to their reliance on complex global supply chains, raw materials, and labor.
2.1 Automotive Industry: Semiconductor Shortages and Production Delays
The automotive industry has been one of the hardest-hit sectors. The global semiconductor shortage has forced car manufacturers to halt or slow production across major markets.
Car makers like Ford, General Motors, and Toyota have been particularly affected, as modern vehicles rely heavily on semiconductor chips for systems like infotainment, navigation, and even safety features such as airbags. This shortage has caused automakers to cut back on vehicle production, leading to fewer car models being available and higher vehicle prices.
2.2 Electronics and Technology Sector: Chip Shortages and Supply Delays
The electronics and technology sectors have also been severely impacted by the semiconductor shortage, which has delayed the production of smartphones, computers, gaming consoles, and other consumer electronics.
Technology companies like Apple, Samsung, and Sony have struggled to maintain production schedules due to difficulties in sourcing the necessary chips for their devices. This has resulted in product delays, limited stock availability, and price increases for tech products.
2.3 Retail and Consumer Goods: Price Inflation and Inventory Shortages
Retailers and consumer goods manufacturers have experienced both price inflation and inventory shortages. Supply chain disruptions have made it harder to source products, and rising shipping costs have increased the prices of goods. Retail giants like Walmart and Target have been impacted by delays in sourcing popular products, such as electronics, furniture, and apparel.
Moreover, the holiday season often sees an uptick in demand for consumer goods, but many retailers were left scrambling to meet the surge in orders due to shipping delays and inventory shortages.
2.4 Food and Agriculture: Supply Chain Vulnerabilities and Price Increases
The food industry has also faced significant challenges, especially in terms of labor shortages, shipping delays, and inflationary pressures on raw materials. The shortage of workers in agriculture, combined with disruptions in transportation networks, has led to delays in food processing and higher prices for many essential goods.
Additionally, climate change and natural disasters have disrupted agricultural production, exacerbating food shortages and increasing the cost of commodities like wheat, corn, and vegetable oils.
2.5 Pharmaceuticals: Supply Chain Disruptions and Raw Material Shortages
The pharmaceutical industry has struggled with supply chain disruptions and shortages of critical raw materials. This has been especially true for vaccines and personal protective equipment (PPE), which saw unprecedented demand during the pandemic. Disruptions in the production of active pharmaceutical ingredients (APIs) and delays in global transportation networks have resulted in drug shortages and delayed vaccine distributions in some parts of the world.
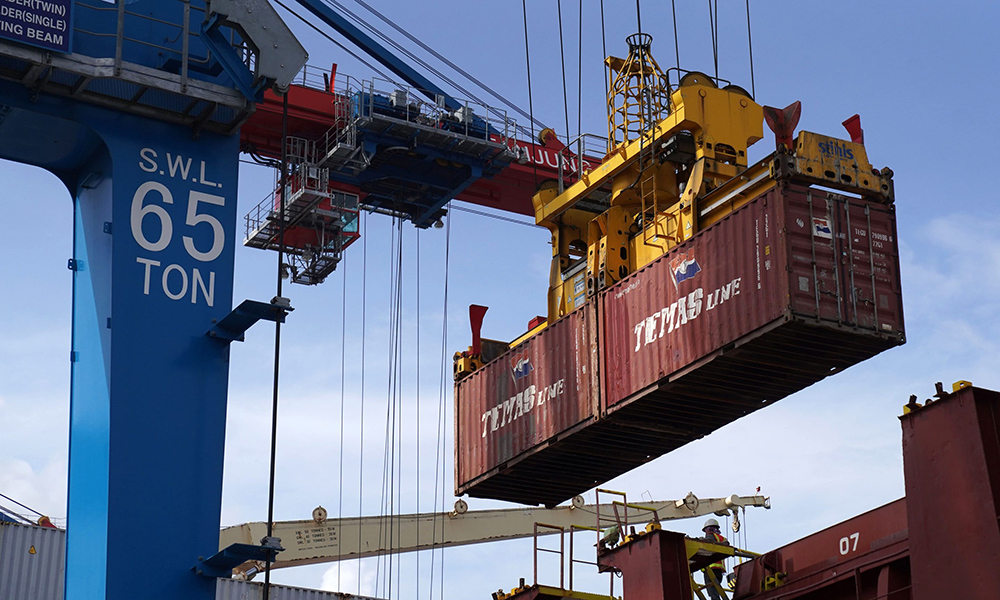
Chapter 3: What Lies Ahead? The Future of Global Supply Chains
The future of global supply chains will likely be shaped by several trends:
- Diversification: Companies may move away from single-source suppliers and adopt nearshoring or reshoring strategies to reduce dependency on distant manufacturing hubs. This could lead to more localized production and sourcing.
- Automation and Technology: The adoption of automation, artificial intelligence, and blockchain technology will help streamline supply chain operations, improve transparency, and reduce inefficiencies.
- Sustainability: Increasing pressure from consumers and governments will drive industries to focus more on sustainable practices, reducing waste and carbon footprints in the supply chain.
- Resilience: As the world faces new challenges such as climate change and geopolitical risks, companies will need to build more resilient supply chains that can withstand shocks.
The global supply chain crisis has highlighted the vulnerabilities of interconnected systems, but it also presents an opportunity to rethink how global trade and logistics are organized for the future.
Conclusion: A Wake-Up Call for a New Era of Supply Chain Management
The global supply chain crisis has exposed vulnerabilities in the way goods and services move around the world. While the pandemic acted as a major catalyst for these disruptions, the crisis is a product of longstanding issues such as over-reliance on globalization, labor shortages, and environmental challenges.
As industries look to recover from the current crisis, they must adapt to new realities and invest in creating more resilient, flexible, and sustainable supply chains. Whether the future will bring complete industry shifts or a return to stability remains to be seen, but one thing is clear: the global supply chain will never be the same again.